Experience tells us that the key to success is providing the right quality of product in line with market requirements. At iSERVICE.asia we have built a rigorous and experienced quality management team, with a third of our employees working in the first line of production: in production workshops, laboratories and inspection stations.
As our experience has shown, even the best factories must be continually monitored and managed to ensure the highest level of on-going product quality. Fluctuations in production volume, Changes to equipment, changes and improvement to production processes can all have a positive effect on product specification and quality, but can also have a detrimental effect on overall product quality. So iSERVICE.asia continues to manage all its manufacturers to maintain the highest level of product quality.
Source Control
1. Almost all products selected by iSERVICE.asia are mature, market tested and proven over the long term.
2.Any new to market products are rigorously tested and assessed by our senior QA engineers before being selected and offered by iSERVICE.asia.
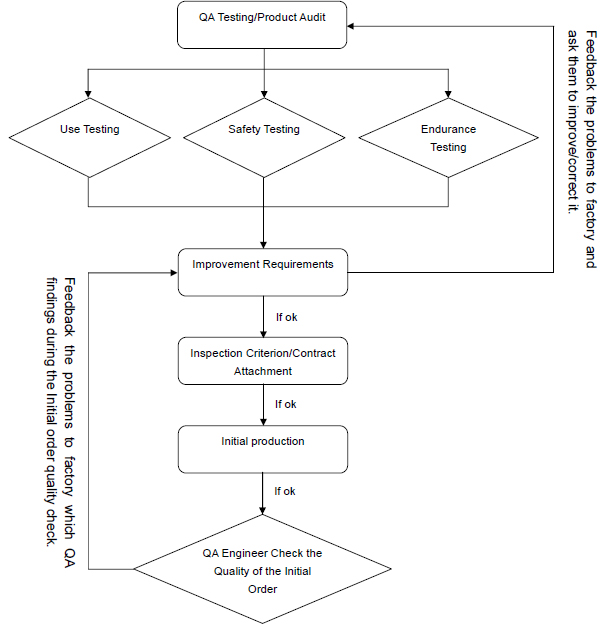
3. iSERVICE.asia can work effectively with any third party agent to complete the process of product approval, certification and certification, (for example - TÜV Rheinland,TÜV PS, BV, UL, ITS)
4. iSERVICE.asia's engineers continually monitor and regularly audit all our manufacturers quality systems and work with them to continually improve.
1. iSERVICE.asia generates and maintains rigorous and fully up to date technical files for every product. This documentation is produced by the sales managers and the QA engineers who are responsible for the products assessment, development and testing. The technical files cover all-important technical details of product safety, Environmental conformance, product performance, life span, and appearance. All of our manufacturers use this document as a standard for purchase, inspection and production, this significantly reducing the likelihood of below standard products. In addition, the technical files are used iSERVICE.asia's QC engineers as the final inspection standard.
2. For all new products, The iSERVICE.asia team fully assess the production process, component level quality inspection, pre-mass assembly inspection, assembly process audit and final inspection, and continue to assess product quality through random testing taken from the production lines.
3. In the event of an upgrade in product components, or in the event of an upgrade in manufacturing process, iSERVICE.asia will fully asses and test the quality of the product, to ensure the benefits of any upgrade are passed on, with no detrimental effect in product performance or quality.
Result Control
1. For every order, iSERVICE.asia's QC engineers ensure conformance in product safety, performance, Environmental friendliness, appearance, and packing quality according to MIL-STD-105E standard.
2. In the event of any defective order that requires rework, iSERVICE.asia repeats the full inspection according to MIL-STD-105E standard, and will inspect the replacement of defective parts particularly.
3. iSERVICE.asia continuously monitors product quality by randomly selecting mature products from repeated orders, to perform the same rigorous testing time and again.
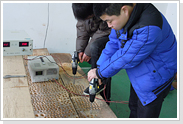
Use Testing
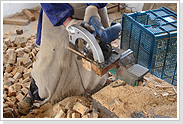
Use Testing
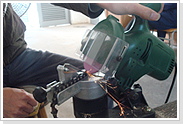
Use Testing
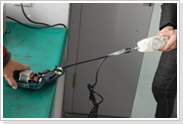
Safety Testing
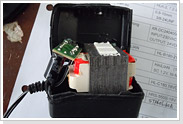
Safety Testing
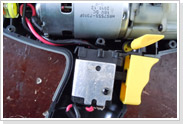
Safety Testing
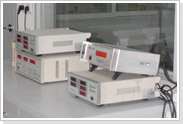
Endurance Testing
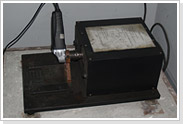
Endurance Testing
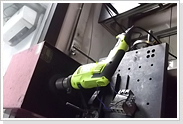
Endurance Testing